-
Jiao 65-2 (Bajiaochang Field, Sichuan)Abstract:
Top Well was contacted by Burlington Resources regarding isolating the wellhead of a recently fractured well. After the fracture treatment, there were found to be two problems with the well head.
Details
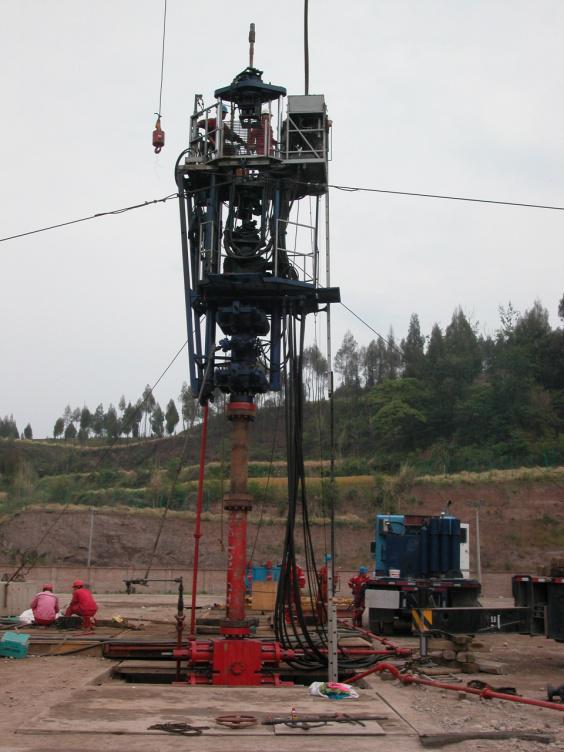
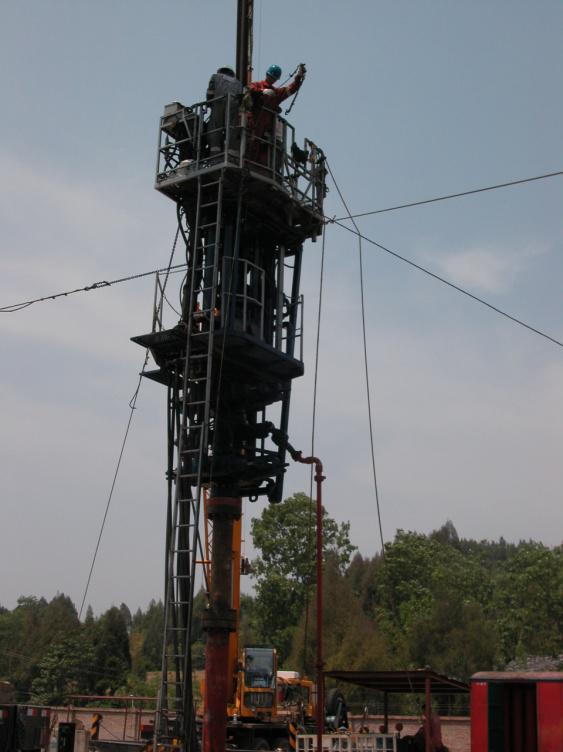
Top Wells S-9 Snubbing Unit in Self Contained Mode
Synopsis: Isolate Well bore to Repair Casing Valves/Wellhead
Well Data:
- Tubing: 60.3mm (2.375”)
- Casing: 139mm (5.5”)
- Max Pressure Possible: 12 Mpa (1740 Psi)
- Well Depth: 3100 Meters (10,170’)
Top Wells technicians looked at the job, and recommended the use of our S-9 unit in “self contained” mode. Because there was very little pipe to be actually tripped during the job, the extra cost of the conventional workover rig was deemed unnecessary. A crane was used to place the BOPs and snubbing unit onto the well. Additionally, the crane was utilized as a gin pole to facilitate picking up and laying down pipe and other equipment from the basket of the snubbing unit.
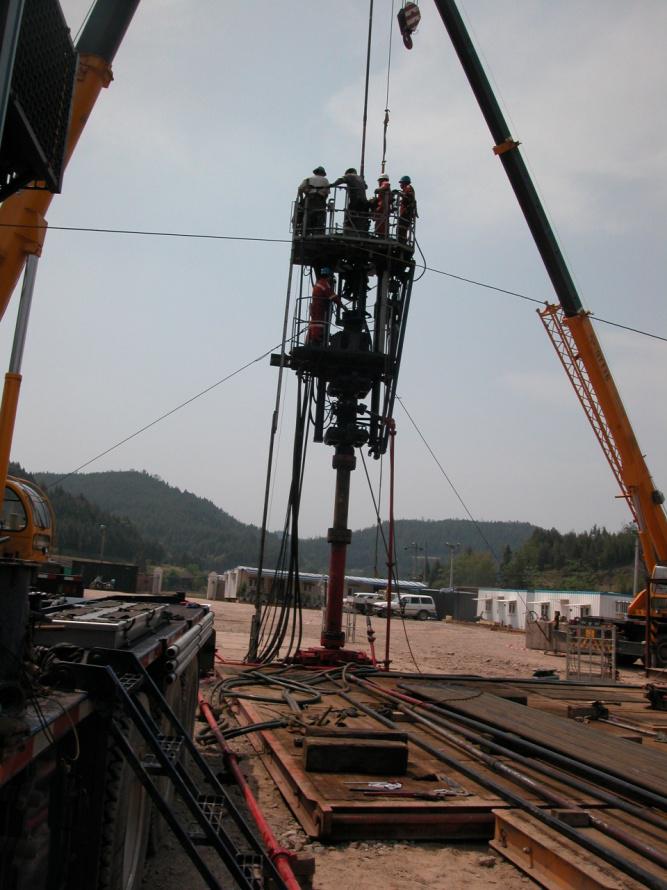
Two tubing plugs were set in the tubing string and the tubing was bled off to zero. The well head was removed above the tubing hanger and the following BOP configuration was installed and pressure tested to 35 Mpa (5K):
From the bottom up:
- 10M {70 MPA} Flow Cross c/w 10M {70MPA} double Gate Valves both sides
-
10 M{70 MPA} double gate BOP
- Bottom Cavity dressed with Blind rams
- Top Cavity dressed with 60.3mm (2.375”) safety fronts
- 10 M {70 MPA} single gate BOP dressed with 60.3mm (2.375”) stripping fronts
- 10 M {70 MPA} x 1.82 m (6’) Spacer Spool
- 10 M {70 MPA} x 1.24 m (4’) Spacer Spool
- 10 M {70MPA} x 5M {35MPA} crossover (DSA)
- 5M {35MPA} snubbing unit dressed for 60.3mm (2.375”)

Staging in Packer
Once the packer was deployed into the well, the snubbing unit tripped in another 15 joints. The packer was then set and the well bled off. A pump was aligned to the casing side and the casing above the packer filled with a methanol/water mix. The packer was tested from above to 18 Mpa (2600 Psi). This represented a 7 Mpa (1000 Psi) differential across the packer.
At this point, attempts were made to try and retrieve the “VR” protection sleeves from inside the tubing spool prep, but the well head was found to be damaged. The decision to replace the entire tubing spool was made. The snubbing unit disconnected the string from the packer using the on/off tool. The string was tripped out and the snubbing unit and BOPs removed. A new tubing spool and valves were installed and pressure tested.
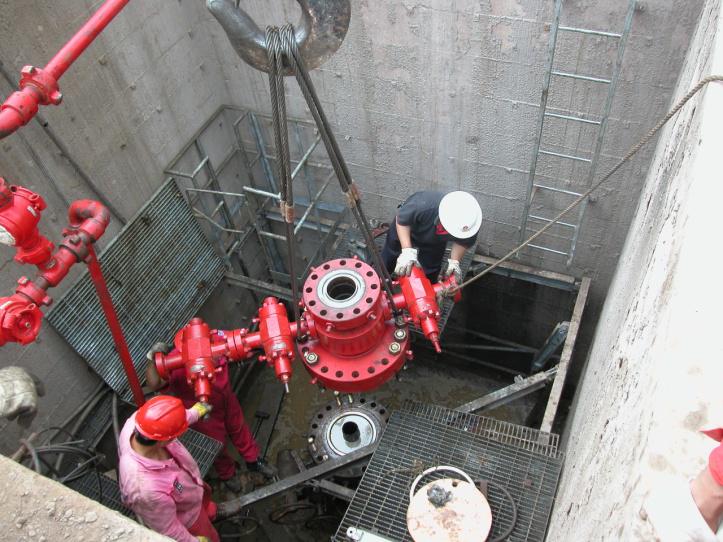
The same BOP stack configuration was rigged in again and pressure tested. The tubing was tripped back in and re-latched onto the packer. The pump was used to equalize the packer prior to unsetting and retrieving the packer. Once the packer had been staged out of the well, the tubing was run back in the hole to its original depth and the tubing landed. All equipment was rigged out, and the wellhead reassembled.
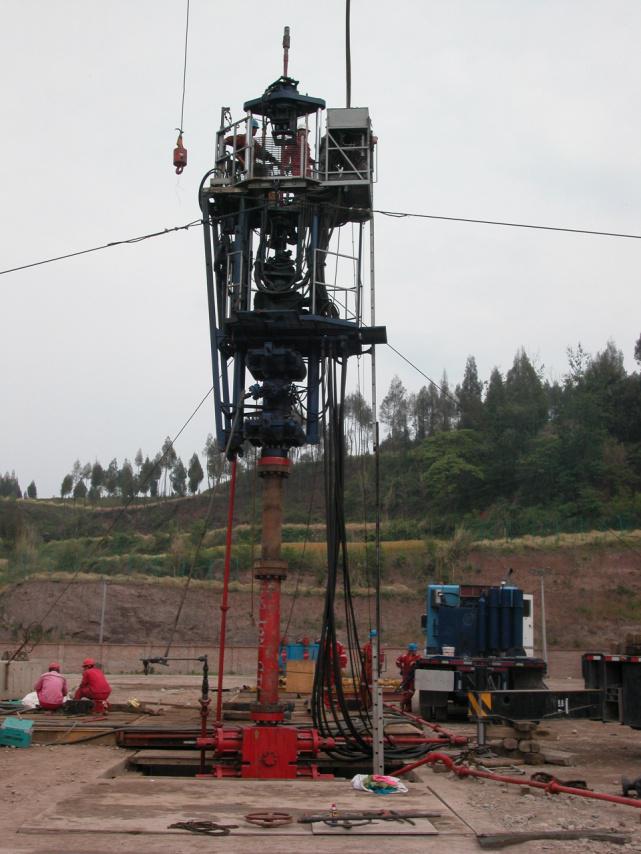
Snubbing Unit Tripping Pipe Into Well